Have you ever wondered what the deciding factor is for the success of a construction project?
Well! Keep in mind that an accurate construction takeoff is the answer.
This process converts the business’s construction plans into specific estimates of materials, labor, and other resources needed for the construction project.
Let’s dive right in.
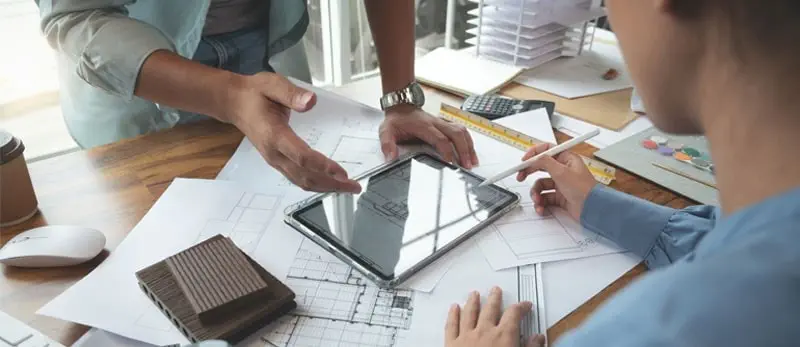
1) What Is a Takeoff in Construction?
A takeoff in construction refers to a term used to describe a method of determining the amount and cost of materials and labor needed for specific projects.
This is like making a list before going to the grocery store. A takeoff enables you to determine the quantities of materials like concrete, wood, steel, or even machinery needed for the project.
It helps you prepare a budget for the labor and other expenses for the project.
To ensure measurement accuracy and prevent cost overruns, adherence to an expert-validated accurate estimating guide is essential for this phase of operations.
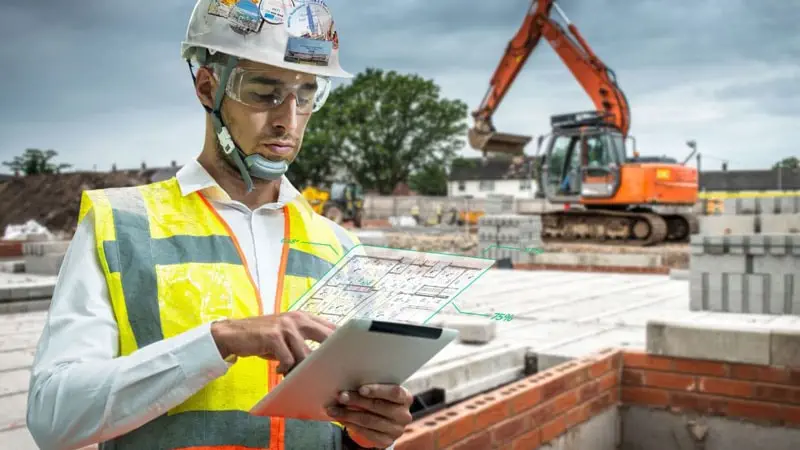
Importance of Takeoffs
In order to successfully win bids and maintain your budget for various construction projects, it is essential to integrate construction takeoffs.
Let’s explore how takeoffs ensure success for a project.
Accurate Cost Estimating process:
An accurate takeoff allows you to estimate your supply needs with precision.
Actually rising material costs is very problematic for construction professionals or contractors. However, now say goodbye to over-purchasing and financial waste owing to takeoff process.
You can now bid soundly based on the figures that you had calculated. Thus, you can better evaluate your project costs.
Better Bidding Strategy:
Too high of a bid loses the job, and too low of a bid loses money. A thorough takeoff allows you to capture that sweet spot so you can always remain competitive without losing the trust of your client.
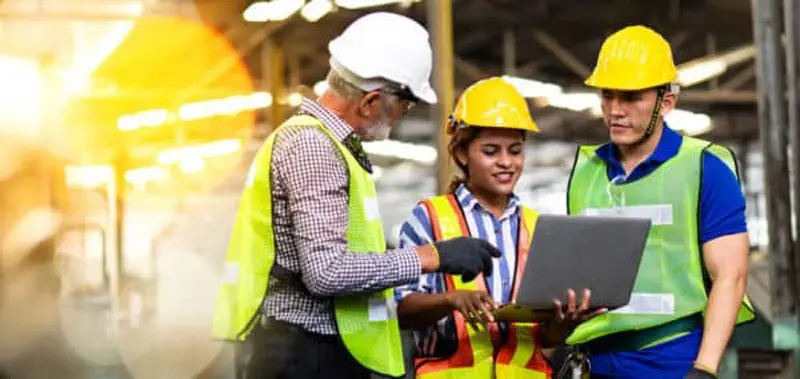
Smarter Plannigng and Procurement:
Good takeoffs allow suppliers to purchase the exact amount of materials without risking shortages or excess supplies which can lead to waste.
Being able to lower your material levels being sent to landfill allows you to aid sustainability in construction.
Boosted Productivity with Online Tools:
With digital takeoff software, there is no need to waste hours measuring off a paper blueprint. It enables you to calculate how much material amounts needed within the blink of an eye. This allows you to save both time and keener, as compared to manual takeoffs.
Now, meeting tight deadlines is a breeze when you’re able to work more swiftly by knowing accurate measurements of everything required for your project.
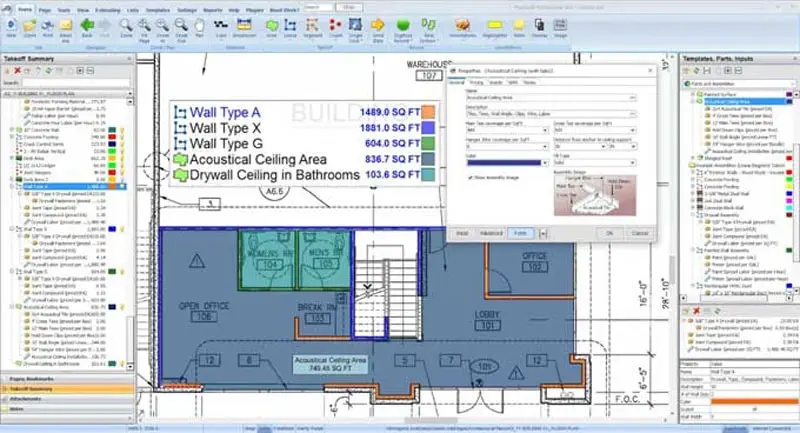
Accurate and Professional Bid Proposals:
Clients will be impressed by your polished, professional proposals when you are able to create them with a clear and elaborate takeoff.
Not only will your competition set the bar lower for you, but you will also find it simpler to win additional jobs.
Enhances Communication With Team Members:
Takeoffs are not only limited to estimators. They can help to keep the entire team which includes architects, engineers and even project managers synchronized & updated.
Cloud-based takeoff software allows for seamless collaboration in real-time. This way, there is less chance of making mistakes or miscommunication.
The accuracy and cost-effectiveness of construction takeoffs make them a beneficial tool in streamlining your workflow. No matter you are a project manager, contractor or estimator, takeoffs will guarantee your success in the construction industry.
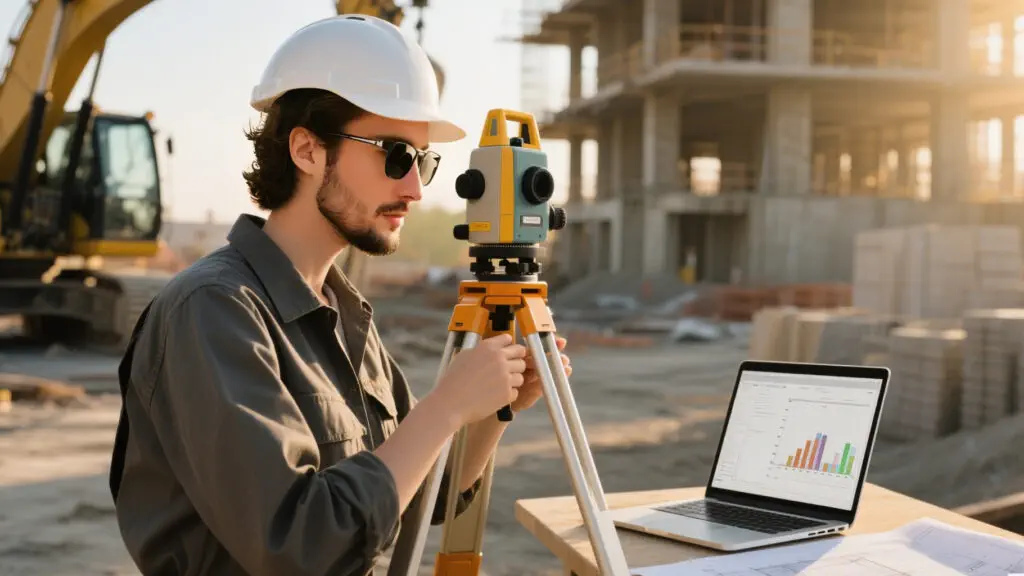
The accuracy and cost-effectiveness of construction takeoffs make them a beneficial tool in streamlining your workflow. No matter you are a project manager, contractor or estimator, takeoffs will guarantee your success in the construction industry.
2) Key Components of a Construction Takeoff
A construction takeoff is a sufficient breakdown of the important information of construction estimation process, such as materials costs, labor costs, equipment, time, and other factors.
Let’s look at the details.
Materials: A material takeoff (MTO) is the most important aspect when estimating all the materials required for your project like cement, steel, or windows. It lists the type and specifications of materials along with the quantity required.
The MTO has 4 key measures:
- Counting (individual items)
- Measuring area (flooring)
- Measuring volume (such as concrete)
- Measuring length (such as pipes and cables)
This avoids situations where materials are in short supply, surplus, or society incurred unplanned expenses, thus aiding in efficient planning, cost estimated and overall project management.
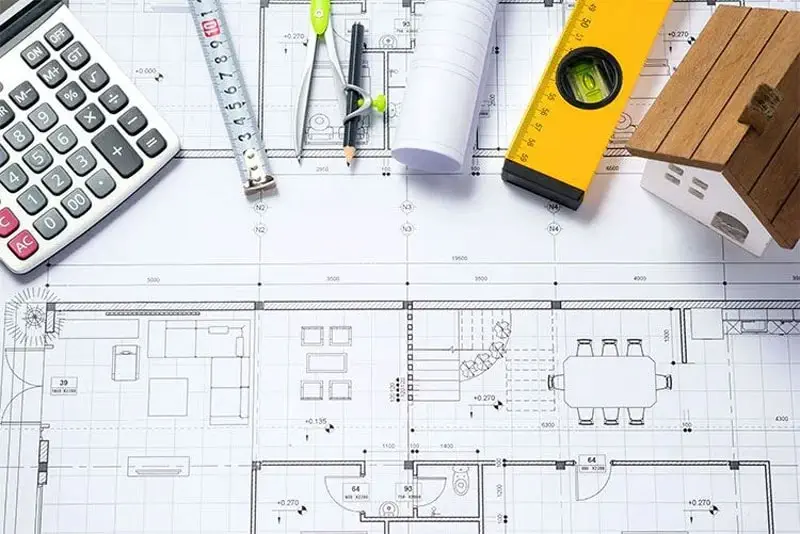
Labor: A precise estimate of the number of workers and amount of time required to complete each task must be estimated correctly.
You have to deal with different categories like electricians, carpenters, and general laborer regarding the amount of work and their respective rates including overtime.
These estimates on labor costs allow you to structure your workforce more effectively and avoid unnecessary costs.
Equipment: Tools and machinery needed for your project which include cranes, drills, and scaffolds are highly significant.
Keep in mind the cost of purchasing the machinery, fuel, and maintenance. Proper estimating and planning of equipment requirements guarantee that all needed tools are in possession so you do not encounter any costly delays due to inadequate or incorrect machinery.
Time: Estimating the time duration for covering each project phase such as setup, implementation, and the final inspection is critical.
You must consider potential external delays because of weather conditions, site conditions, or even unplanned situations.
Accurate time estimates help meet set targets as well as eliminate the need for extra costs due to overtime.
Other Considerations: Consider and account for waste, material management loss, and even challenges on weather conditions or access on-site locations.
Mitigation plans for such factors should help guarantee constraints such as budget remain intact and delays that were unexpected get accommodated.
When planned properly, you can deal with changing and unpredictable conditions keeping control over the scope, timelines, and cost of projects.
3) 6 Steps to Complete a Construction Takeoff
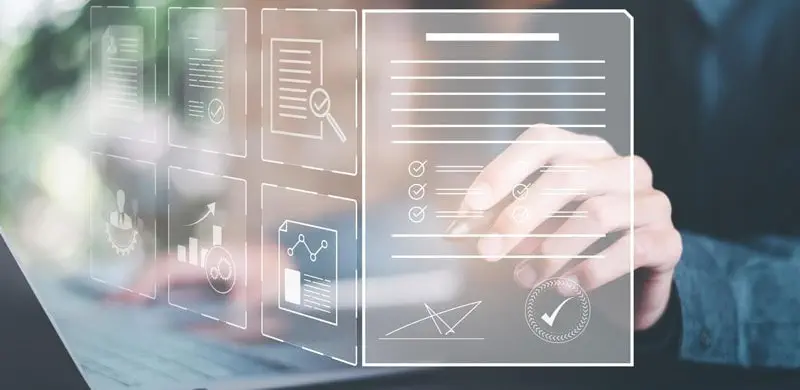
In order to facilitate an accurate takeoff to set up your project for success, you have to follow these six steps.
Step 1: Review Project Documents
In order to measure or count anything, you must first get a hold of the project.
Begin by closely examining the construction drawings, specifications, and other project documents as they outline material requirements, component dimensions, and special instructions.
You will avoid mistakes by using paper blueprints while reviewing all components, and with digital blueprints, all the important information is provided to you.
Step 2: Identify Quantities
Next comes a list of materials needed for the project, similar to a grocery list that needs to be checked off. Concrete, lumber, steel, and screws must be included in the list.
This process is known as quantity takeoff, and its goal is to ensure that nothing is overlooked. Missing materials will slow down the construction or lead to a budget overreach.
Construction takeoff software can assist in tracking materials more effectively which minimizes error.
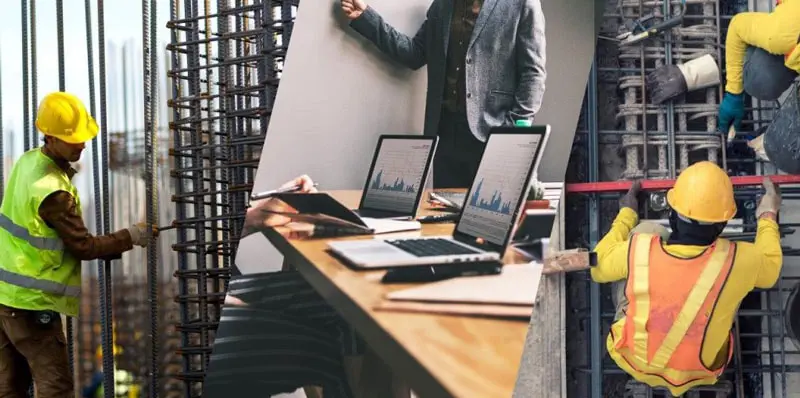
Step 3: Measure Dimensions
It’s finally time to take your measurements. You have to establish the precise amounts that you need for each material.
For paper blueprints, a scale ruler will assist you in taking measurements for square footage, surface areas, and lengths of beams among others. For digital takeoffs, estimation software will allow you to perform the aforementioned actions with even more efficiency.
Step 4: Create a Takeoff Sheet
After you are done gathering relevant components, depict them concisely on your takeoff sheet.
The sheet must highlight each material alongside its respective quantity and any additional remarks.
As an example, all wood parts could be grouped in one subsection along with all electrical pieces in a different one.
A well-organized take-off sheet facilitates data usage for project estimations and planning purposes by contractors and estimators.
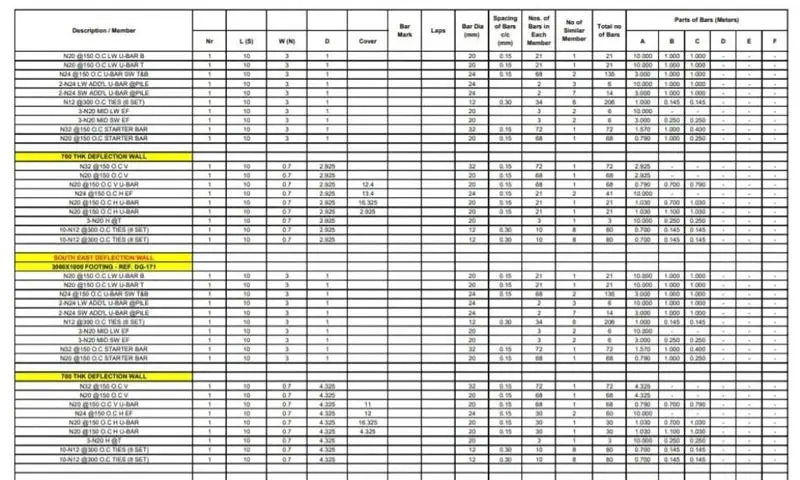
Step 5: Verify’ s Calculation Review
The mistakes made in a construction takeoff may give rise to numerous problems.
Therefore, check unit costs, adjust for waste, and double-check your calculations. Taking paint as an example, add extra coats or touch-ups for the windows and doors.
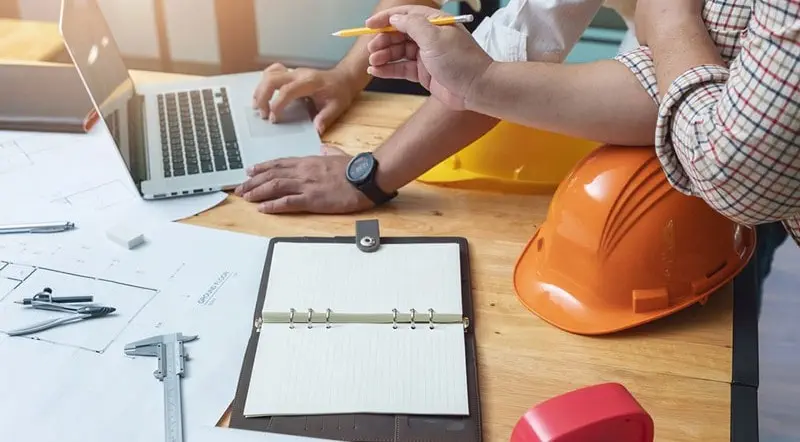
Step 6: Compile and Review
Putting all the pieces together in a comprehensive takeoff document and final cross-comparison with project specifications is the last step. Missing components, if any, can be added in this step.
Construction documents usually include details like takeoff quantities where construction takeoff estimate errors mean material shortage or excessive outlay.
A check shall be done with project supervisors or personnel in charge of the construction activity to see the f submitted numbers are reasonable. A comprehensive takeoff document aids the efficient management of construction projects, keeping in focus the financial constraints.
In a nutshell, I must say that the manner in which you perform a takeoff does not matter while precision in estimation is vital in order to prevent unwanted delays and issues and guarantee maximum efficiency of the project.
4) Tips for Successful Construction Takeoffs
An accurate construction takeoff is essential for effective project execution.
Mistakes at this level of construction project planning lead to insufficient materials or ballooned expenses.
The following guidelines will assist in achieving cost-effective estimates.
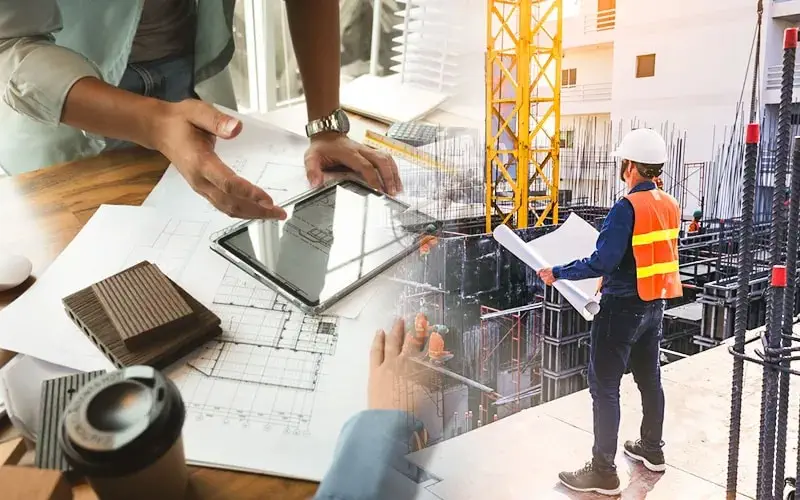
Stay Organized: To take off successfully, you must always remain organized.
Do not forget your takeoff sheet and ensure it has all materials, labour costs, and other project expenses included.
Look over your project documents, check that information is stored securely, and update records if applicable.
Remember, a properly organized takeoff saves time and minimizes unexpected challenges.
Leverage Technology: Digital takeoff software can reduce the workload significantly. Calculating material quantities using a physical blueprint is tedious, While these construction estimating software are much faster and have less margin for error.
Estimation accuracy improves drastically. Simple integrations allow contractors to revise takeoffs at any point during the change to a project.
Collaborate with Team Members: There’s no need to work single-handedly. Collaborating with different engineers, architects and other experts in the construction field will allow for an amalgamation of knowledge which will increase the likelihood of success in the project.
Sharing information ensures that all of the correct decisions are implemented, and client budgets are maintained. Effective communication goes a long way in avoiding issues and smoothens the project workflow.
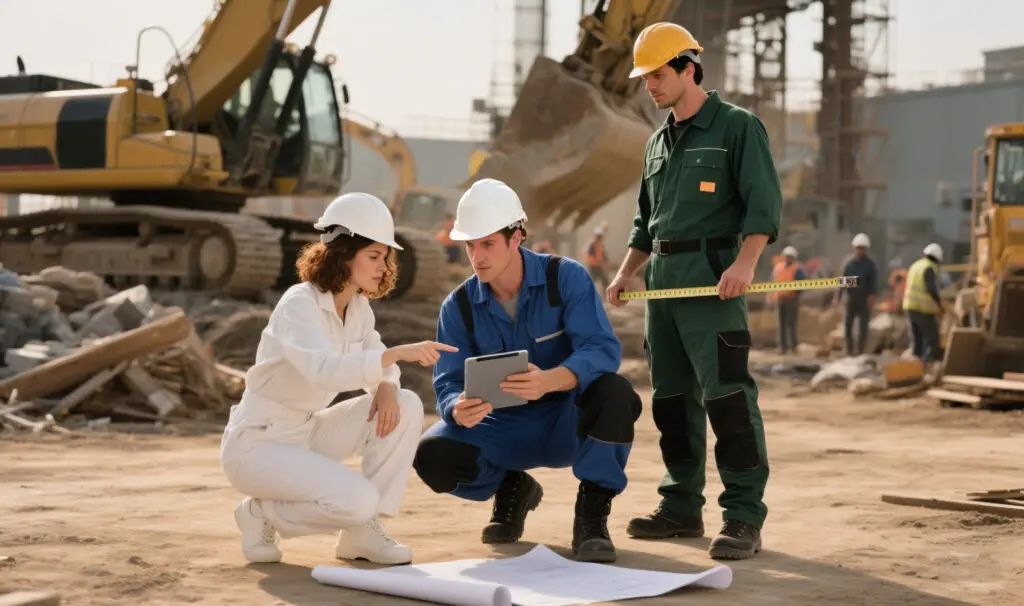
With the aid of technology and teamwork, satisfying takeoffs can be accomplished.
This results in precise estimates, fewer human errors, and a better overall experience during the construction phase.
Conclusion of Construction Takeoff
From the above discussion, we have concluded that to estimate the project correctly, construction takeoffs are very imperative.
Making use of a logical sequence improves your cost control, error elimination, and bid strategy.
Moreover, it is possible to enhance speed and increase accuracy by simply using the right tools and being organized. Don’t let miscalculations hold you back—embrace efficient estimating to boost your success.
What are you waiting for? Contact Everstar today to get guidance from our experts and the right construction machines for your project.
FAQs
1. What is a construction takeoff?
A construction takeoff is a method by which you estimate the amount of material and labor required for a construction job based on the project documents provided.
2. Why are takeoffs important in construction?
In construction, the takeoff process is important in providing accurate estimation as well as resource allocation which subsequently impacts budget and timelines. Takeoffs help facilitate a project’s smooth and efficient run.
3. What tools can I use for construction takeoffs?
You can use a wide range of scale rulers, digital measuring tools or even specific takeoff gadgets for speed and accuracy.
4. How can I ensure accuracy in my takeoffs?
For accuracy, you must provide confirmation of cross-verifying the relevant project documents, having the correct calculations, and the necessary teamwork integration for comments and approvals.
5. Can Everstar provide assistance with construction takeoffs?
Yes, Everstar can help with construction takeoffs with the addition of some resources like reliable tools and equipment’s or experts’ guidelines needed for your construction project that help ease the takeoff process.