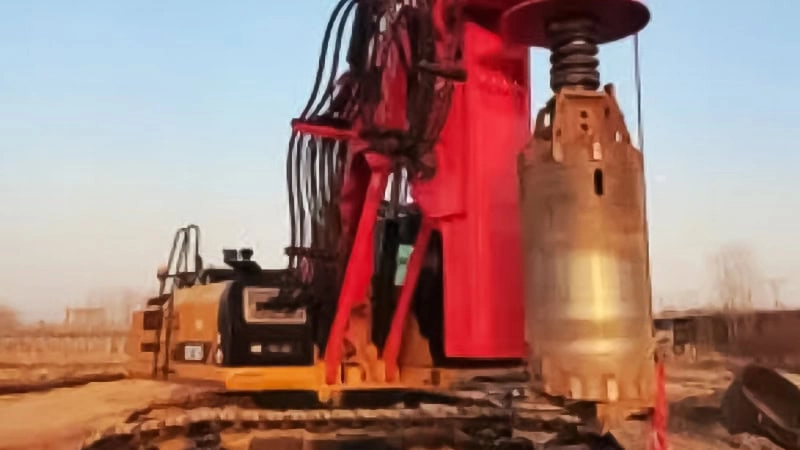
Key Takeaways
- Match tools to ground conditions: Use auger bits, core barrel, or belling bucket depending on soil type and project needs.
- Ensure equipment compatibility: Make sure the drill pipe and other tools are properly attached to your drilling machine or hydraulic rig.
- Use the right method: Rotary drilling creates structural hole accuracy while core drilling focuses on precision process and clean sampling.
- Maintain your tools: Clean, inspect cutting edges, and lubricate regularly to prevent broken parts and extend service life.
- Train your crew: Well-trained operators improve safety, tool handling, and performance under heavy downward force.
As infrastructure development demands increase globally, drilling tools play a growing role in both mid-scale and small-scale construction. From roadworks and bridge foundations to utility lines and geotechnical investigations, the right drilling equipment is essential to getting the job done safely, productively, and cost-efficiently.
Beyond traditional construction, drilling tools are also central to exploration and production activities in mining, oil and gas, and groundwater development. These operations require precision and durability under varied geological conditions, depending on soil type, depth requirements, and project goals.
Because drilling requires technical expertise and reliable equipment, choosing the right tools and proper equipment placement is essential to minimize downtime. Everstar Machinery’s mission is to support contractors with compact, efficient solutions designed for today’s job site challenges.
In this article, we will explore common drilling tools, including auger bits, core barrels, and the drilling machines that power them. We’ll examine rotary and core drilling methods and discuss key factors such as tool selection, maintenance, and operator training.
Understanding the Basics of Drilling Tools
Drilling tools are critical for foundational work, soil stabilization, and pile installation. These components cut, break, and remove ground material to create precise boreholes or drilled shafts.
For example, during bridge construction, using the right attachments ensures the soil is penetrated and stabilized to form a solid base.
When installing utility poles or deep piles, equipment must handle a combination of various soil conditions—such as soft clay or dense gravel—without premature wear or failure.
The performance and durability of these tools generally directly affect project timelines, safety, and costs. Poor tool selection can hinder progress, increase maintenance requirements, and pose safety risks to site crews.
Drilling Machine and Its Role on the Jobsite
Drilling machines provide the mechanical force needed to drive tools, such as auger bits and core barrels. Whether mounted on rigs or used as standalone units, they convert rotational power into cutting action, enabling efficient and accurate ground penetration.
In mid-scale projects, compact rotary drilling machines are often preferred for their ability to operate in confined spaces and adapt to a range of ground types.
Their compatibility with specific attachments, torque output, and overall configuration plays a major role in drilling machine productivity and drilling precision.
Materials and Engineering Considerations
Drilling tools rely on high-quality steel grades, heat treatment, and precise geometry to ensure durability and performance. Hardened steel resists wear in abrasive soils, while cutting edge design improves penetration and material removal.
Tools must also be compatible with rotary drilling rigs and mid-scale equipment to ensure secure fitting and smooth operation. Proper material selection and engineering help reduce downtime, extend tool life, and improve overall drilling efficiency across various construction and resource projects.
Overview of Drilling Bits and Their Uses
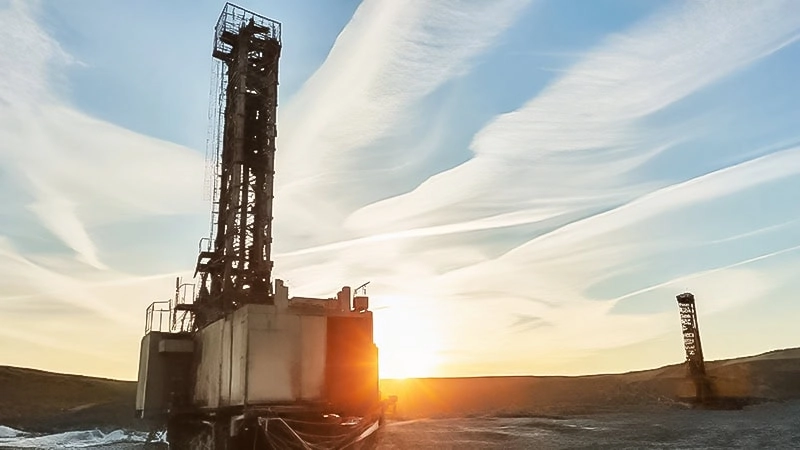
Drilling bits are key components in any drilling operation. As the cutting tools at the end of a drill string determine how effectively the equipment penetrates different materials.
Selecting the appropriate bit for the ground conditions and project objectives is crucial for achieving efficient, safe, and cost-effective drilling. Common types typically include:
- Bucket tooth rotary buckets: Ideal for various drilling applications, these tools provide efficient material removal and enhanced productivity.
- Auger bits: Suited for soft or loose soil, these efficiently remove debris while maintaining borehole stability under the load of the drilling machine.
- Rock bits: Built for hard rock conditions, these durable tools (such as roller cone or PDC bits) deliver high penetration rates in mining, oil, and gas applications by rotating at optimal speeds.
Matching Drill Bit to Soil and Rock Conditions
Soil type, rock hardness, moisture content, and abrasiveness all influence the process and performance of the bit. For example, clay can clog standard bits, while abrasive sandstone requires wear-resistant materials.
Matching the bit’s shape to the site conditions ensures clean penetration, longer tool lifespan, and fewer disruptions.
Contractors also need to balance performance with cost. Choosing bits that offer durability over time reduces replacement frequency and minimizes downtime.
When to Use a Drilling Bucket
Drilling buckets are specialized tools for removing soft, loose, or cohesive soils—especially in conditions where auger bits might lose efficiency. Instead of cutting, buckets scoop material and retain it until extracted.
They’re ideal for creating wide-diameter boreholes in foundation work and for clearing out partially collapsed shafts. Equipped with bottom gates and replaceable cutting edges, belling buckets are compatible with rotary rigs and reduce hole wall disturbance during excavation.
Rotary Drilling Tools for Foundation and Utility Work
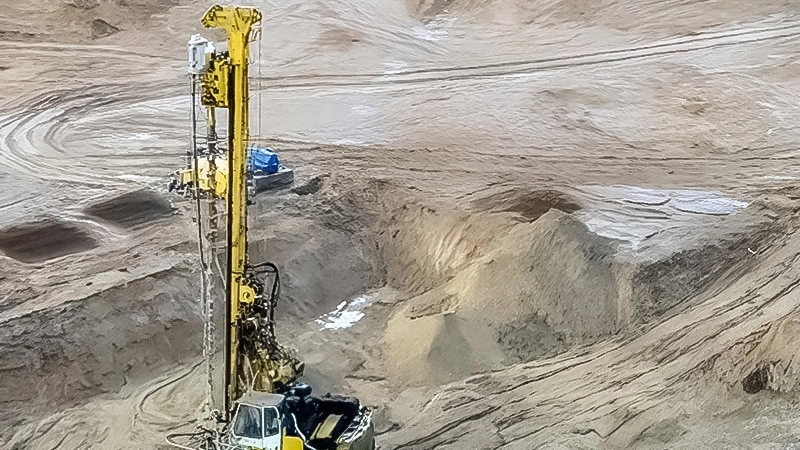
Rotary drilling tools play a crucial role in foundation construction and utility installation, including water lines, electrical conduits, and sewer systems. These systems enable vertical, precisely aligned boreholes to meet the tight specifications of modern infrastructure.
Rotary tools maintain steady rotation and downward pressure, helping contractors drill consistently through various ground materials. This consistency improves structural reliability and reduces errors in component placement.
Everstar Machinery focuses on compact rotary rigs that integrate seamlessly with these tools. Our equipment provides contractors with the flexibility and reliability required for mid- to small-scale jobs, while maintaining strict safety and quality standards.
Importance of Accurate Drilled Holes in Construction
Accurate drilled holes are fundamental to the industry quality. Misaligned or irregular boreholes can compromise structural integrity, interfere with reinforcement placement, or disrupt utility alignment.
Rotary drilling systems support accuracy by maintaining constant rotational speed and pressure. This produces clean, vertical holes with smooth walls—essential for concrete casting, rebar placement, or utility insertion on any surface.
High-quality holes reduce rework and support long-term structural performance.
Optimizing Performance with Rotary Systems
Several variables affect rotary drilling efficiency, including torque, rotation speed, and soil interaction. High torque improves performance in dense soils, while controlled speed reduces wear and enhances cutting action.
Regular inspections of drill pipes, bearings, seals, and hydraulic components help identify early signs of wear and tear. Preventive maintenance keeps rigs running smoothly and reduces project downtime.
Additionally, cleaning and lubricating moving parts protects tool lifespan and ensures consistent drilling accuracy.
Attention to operation and upkeep ensures that rotary rigs meet performance standards across varying site conditions, including other materials such as soft limestone or mixed backfill, and maintains the integrity of the bore and drilled hole.
Core Drilling Tools in Construction
Core drilling is commonly used in construction, geotechnical engineering, mining, and material testing. This process involves extracting cylindrical sections of soil, rock, or concrete—known as cores—for analysis or to create precise openings.
Its benefits extend beyond accuracy:
- Core drilling minimizes disruption to surrounding materials;
- Generates less dust and noise compared to other common methods;
- And enables clean sample extraction without damaging surface structures.
These qualities make it ideal for structural testing, anchoring systems, and retrofitting projects where high precision and minimal impact are critical.
Selecting the Right Core Barrel and Bit
Selecting the correct core barrel and drill bit is crucial for obtaining clean samples and achieving efficient performance. Key factors such as core barrel diameter, barrel length, and the materials being drilled directly impact accuracy and tool lifespan.
Larger diameters are often required in foundation assessments or structural shaft sampling, for instance, where complete, undisturbed sections are needed for analysis or anchoring systems.
In contrast, shorter barrels are preferred in confined areas—such as interior retrofits or tunnel work—where space is limited and depth is minimal within each hole.
Choosing the Right Drilling Tools for Your Project
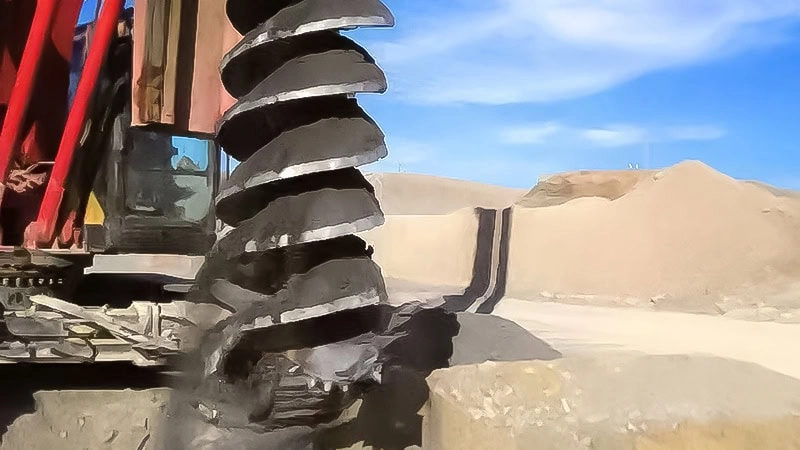
Whether the project involves foundation construction, utility installation, geotechnical surveys, or resource extraction, selecting the right drilling tools starts with evaluating key factors.
Depth, ground conditions, equipment, site access, and budget determine the best tool, whether it is an auger bit, core barrel, or a drilling bucket for loose soil.
It’s also important to consider long-term support. Access to spare parts and reliable local service can make a significant difference when unexpected maintenance is needed or replacements are time-sensitive.
A minor delay due to an unavailable drill bit or drill head can halt drilling operations entirely, impacting both timeline and cost.
Everstar Machinery is committed to providing mid-scale, compatible equipment that supports a wide range of drilling tools, giving contractors the flexibility to adapt tools to real job site conditions and make smarter investment decisions.
Practical Tips for Contractors
Before selecting equipment, it is essential to take time to understand the project scope and ask the right questions when considering which drilling tools to purchase.
Careful consideration of drilling practices, according to the U.S. Geological Survey (USGS), helps prevent mismatches, reduce inefficiencies, and avoid costly delays.
What soil or rock conditions will you encounter? How deep will you need to drill? What equipment is already available on-site, and is it compatible with components like belling buckets, jaws, or drill pipes?
Training is just as critical. Operators and site crews should be familiar with different tool types, safety procedures, and maintenance routines.
Ongoing training not only reduces the risk of accidents but also improves tool handling, especially under high downward force, where sharp edges and welded connections must withstand extreme pressure.
FAQs – Types of drilling tools
What is the most common drilling tool used in mid-scale construction?
Auger bits are widely used in mid-scale projects due to their efficiency in operations through soil and loose soil. They effectively remove debris and maintain borehole stability, making them ideal for applications like utility installations, roadworks, and foundation work.
Can I use rotary drilling tools for hard rock?
Yes, rotary drilling tools equipped with specialized drill bits, such as roller cones or PDC bits, are designed for hard rock formations. They provide the necessary torque and durability to penetrate tough geological conditions common in mining, oil, and gas exploration.
How do I maintain my drilling bits for longer life?
Proper maintenance includes regular cleaning to remove debris, inspecting for wear or damage, and lubricating moving parts. Using the right drill bit for soil or rock conditions reduces excessive wear. Routine care extends bit life, improves performance, and minimizes downtime on the jobsite.
Is core drilling suitable for deep foundations?
Core drilling is ideal for precise sampling and creating openings at moderate depths. While it offers high precision and minimal site disruption, rotary drilling methods are often preferred for very deep foundation work due to greater efficiency over large depths.
How do I know if my drill tool is compatible with my rig?
Compatibility depends on factors like tool size, connection type, and drilling rig specifications. Always consult equipment manuals and suppliers to confirm compatibility. Using tools designed for your specific hydraulic rig model ensures optimal performance and safety and avoids costly mismatches.
Conclusion: Final Thoughts on Choosing Drilling Tools
Choosing the right drilling tools is essential for maximizing efficiency, safety, and cost-effectiveness on any project. Spending time to assess and match tools to specific job requirements results in better outcomes and more seamless drilling operations.
Consulting with experts can make this process easier. Everstar Machinery is committed to offering dependable, compact, and versatile drilling equipment built to satisfy the needs of modern industry.
Call To Action: Ready to Optimize Your Drilling Operations?
Explore Everstar’s comprehensive portfolio and discover a range of drilling accessories and equipment.
Visit the Contact Us section and reach out to discuss the best drilling tools for your next project with our experts.