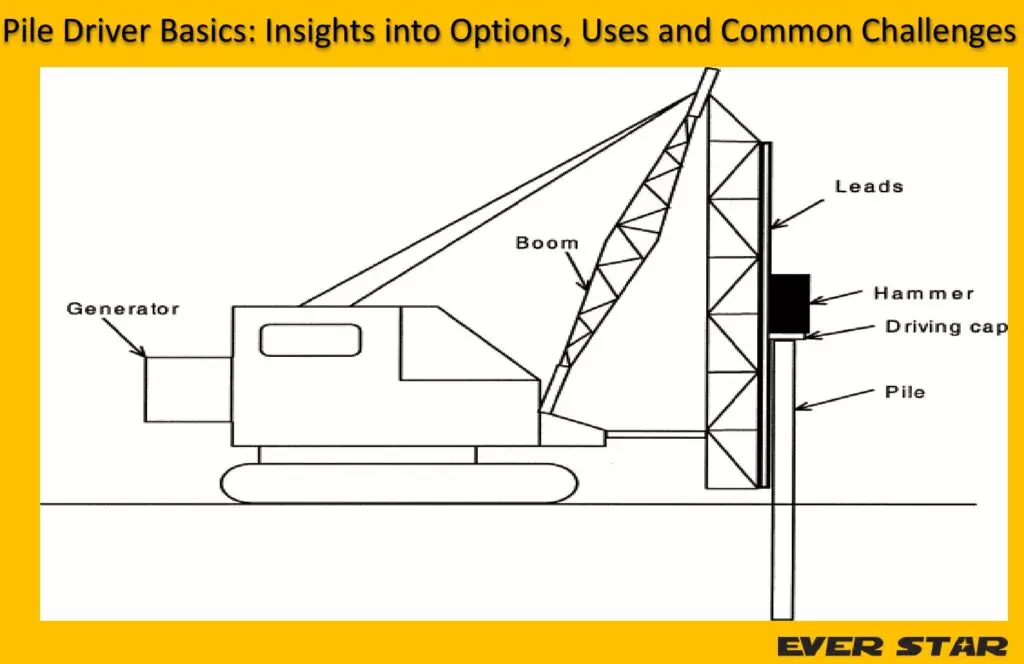
During construction in the olden days, driving timber piles into the ground using bare hands was a common practice. The twentieth century saw the emergence of the hydraulic systems. That laid the ground for modern and ingenious pile driver technologies.
Construction projects rely on piles, the vertical columns that run deep into unexcavated grounds, among other factors. A pile can be any material, from concrete to timber. Some terrains can only support bridges, buildings and other structures through steel piles and different types.
Although the piling technology is centuries old, many people still wonder “What is a pile driver?”. As the methods advance, confusion can emerge. A pile driver is a system that installs piles, and typically comprises a hammer cushion, pile cushion, lead, and helmet, among other components.
As with any other technology, using the pile driver presents various challenges ranging from operational to site-related ones. Identifying and knowing how to counter these challenges can help a contractor optimize pile installation equipment.
In this article, we delve deep into pile driver construction technology, identifying the main uses and common challenges, and sharing some expert tips.
What is Pile Driving?
Pile driving is an installation technique for piles into the ground. Often, the ground has not been previously excavated. It is a systematic construction process that provides a deep foundation for structures. Contractors use machines called pile drivers or pile hammers to install the piles. A successful installation is when the piles reach the planned depth without damage and are rigid enough to support the envisaged structure.
Pile driving is an important process in the construction of bridges and buildings. It is also applicable to the installation of road signs, fences, and barriers. The technology is valuable for a quick installation and minimal environmental disruption.
Considering the inevitable challenges of this process and the high cost of project failure, one should thoroughly plan and execute the piling project. That would include using only the best pile driver machines.
What are the types of pile drivers to consider?
The market offers a variety of pile drivers, each with advantages and drawbacks. As a contractor or project owner, choosing the correct type is fundamental to project success.
If you are wondering about the options, the basic categorization of the designs comprises hydraulic hammer, diesel hammer, vibratory hammer, and impact hammer.
1. Hydraulic hammer
Hydraulic hammers derive their power from hydraulic pressure. The hammer is designed to apply vertical blows on the pile head with the help of a vertical guide. This guide moves up and down, hence hammering the pile to the required depth.
The hydraulic hammer is renowned for unmatched versatility and accuracy. Contractors who want to drive piles with the least noise possible would choose the hydraulic hammer type.
2. Diesel hammer
Diesel fuel is the power source used to drive the piles. These hammers are ideal for heavy-duty jobs. The pile drivers are more cost-effective than hydraulic hammers. With their sturdy construction, these machines are highly durable despite being used in demanding applications.
3. Vibratory hammer pile driver
As the name suggests, the vibratory pile driver installs piles using vibrations. It is a powerful mechanical device working on the principle of sine wave oscillation. It has counter rotating eccentric weights that rotate in opposite directions, creating centripetal forces vertically.
These forces cancel each other out in the horizontal direction, so horizontal vibrations are minimal. The effect is oscillating vertical vibrations that create the necessary vertical force to drive piles.
4. Impact Hammer Pile Driver
For impact pile driving, a powerful drop hammer hits the pile head to drive it into the ground. Its powerful impact block effectively forces the piles into rocky grounds, sea beds, and other hard grounds. This method is notorious for producing a highly impulsive sound that can be heard kilometers away. This would be an ideal method if accuracy is a priority – it accurately adheres to the marked pile locations.
So, which of these types of pile drivers is suitable for your project?
One valuable consideration is the project type. Some pile drivers are only suitable for land-based projects, for example, solar panel pile installation. Others can work in water-based environments.
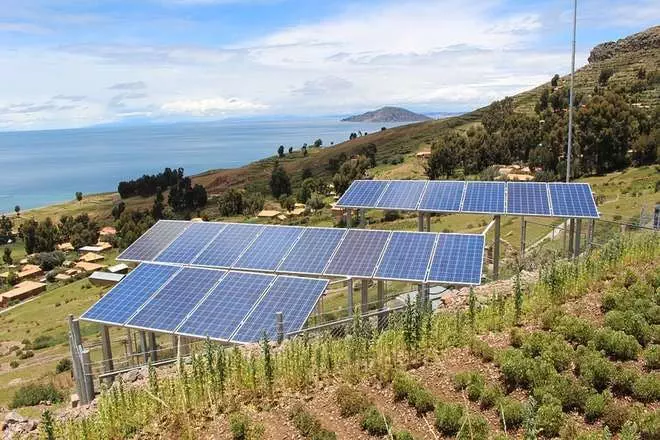
The level of interference with the surroundings is also a big consideration, knowing that some pile drivers are noisier than others. You need to consider your budget. Some machines may be too expensive, yet cheaper ones can still do the job.
Other important points to consider when choosing a pile driver type are the reputation of the quality of the product offered and the availability of after-sales support.
As our experienced agents will tell you, we have some of the most cost-effective and functional types of pile driver machines. Whether you are looking for a portable handheld pile driver or a more dynamic solar pile driver machine, Everstar provides designs to tackle your project.
What is a pile driver? The Components
The Pile Driver Lead
This component guides the hammer and piling. It could be fixed hanging or swinging depending on the suspension style. Its main role is to maintain the synchrony between the hammer and pounding.
The Pile Cushion
When installing concrete piles, it is important to incorporate a cushion between the pile and the hammer. A popular type of cushion is plywood.
The hammer cushion
Often located between the helmet and striker plate, the hammer cushion absorbs the initial striking force from the hammer. This component minimizes damage to the striking parts.
What is the helmet?
This is the part that connects the pile to the hammer system. Thanks to this connection, the head of the pile receives uniform hammer blows. The helmet minimizes pile head damage.
The Power Source
Every pile driver has a power source. The most popular options are electric and diesel power. However, hybrid power machines have emerged to apply the advantages of both power sources.
How does a pile driver work?
The principle of pile driving is the same for most pile driver machines. You create the support column before the work and install it to the ground through the preferred pile driving mechanism.
Looking at the specifics of the pile driving process, there are three methods namely vibro-driving, pressing (jacking), and impact driving. Vibro-driving comprises an oscillating driver. It significantly minimizes vibrations and friction. Impact driving is characterized by a drop hammer that generates impact through a falling hammer. For pressing or jacking, the other piles are instrumental in creating the force. The choice depends on several factors, including the ground conditions.
Common Challenges in Pile Driving
Here are some challenges you are likely to encounter as you drive piles:
Uniquely Shaped Piles
Typical piles are cylindrical, but what would you do if you encountered a different shape, say H-profile? If piles are not the standard design, pile driving can be problematic. There could be costly delays in the project. Experienced contractors know how to counter such unexpected challenges to avoid project delays.
Pile Damage
No matter the pile type, there is always the possibility of pile damage. The damage could occur at the tip or along the length. When a pile is damaged, the load transfer mechanism becomes affected. You can tell a pile is damaged from discolorations, cracks, and reduced capacity.
What’s the best way to deal with this challenge? It all boils down to the pile design and installation method. A good design accounts for the type of pile material, load transfer method, site construction equipment, and site conditions.
Further, you can avoid pile damage by incorporating the correct safety factors and adhering to high levels of quality control. Regular inspections and tests of timber piles and others are crucial for piles that will be installed in the future.
Unexpected soil resistance or profile
A promising pile installation project can suddenly turn hectic and lead to project suspension due to unexpected soil conditions. The soil profile has a direct effect on the pile capacity so you cannot afford to ignore it.
Soil surprises are common in civil engineering works, so solutions have been suggested. For a pile-driving project, the first course of action is to reassess the site conditions. The soil resistance, permeability, compressibility, and other important soil properties must be determined.
If the changes from the original soil conditions are significant, it would be worthwhile to consult an expert. After analysis, the expert may recommend soil stabilization, new foundation design, or even project relocation.
Because of this monumental risk, solid project risk management is recommended. Whatever soil issue may occur, you should have a practical remedy, including the possibility of stretching the project timeline.
Environmental Effects of Pile Driving Activity
With the common interest of safeguarding the environment and growing demand for improved construction environments, the contractor or project owner should prioritize solving any environmental concerns related to using a pile driver.
One of the common concerns is noise. Depending on the method used, piling can produce significant noise. The resulting public nuisance may attract public conflict.
Timely public engagement can manage this challenge. Being open about the expected disturbance, sound pressure, and the exact time the noise impacts are expected can ease the effect.
There are standards about noise limits for construction sites in different regions. You can use such to measure and limit the noise. It is worthwhile to note that the piling process does not have to be extremely noisy. Technology advances have brought much quieter pile drivers. Air and diesel hammer technologies have widely been replaced by the more advanced hydraulic hammer and vibratory pile driver technologies.
Vibration is another environmental challenge associated with pile driving. The vibrations disturb people near the piling activity and risk damage to structures. Again, the relevant standards can help determine the safe vibration level to invest in the right piling technologies from a reputable provider such as Everstar.
Safety Precautions and Maintenance
No matter how robust the pile driver is, the equipment demands safety precautions and regular maintenance.
It is important to maintain the highest level of safety as you drive piles, starting with the site assessment. A thorough site assessment before commencing the work helps identify any risks. Check for unstable soil, debris, and hidden utility installations.
The safety of the pile driver is an equally important area of assessment. Is the equipment well maintained? Are all machine safety components working? Are the personnel handling the pile driver well-trained? Answer these questions before proceeding with the piling job.
One may be trained, but without personal protective equipment, they remain at risk during the piling operation. As required in similar working environments, the operator should wear the appropriate boots, safety glasses, helmet, and high-visibility vest.
To add to the PPEs, the team should also have a proper communication mechanism. The best pile installation contractors have radios for communication and supplement that with hand signals. This ensures there is always a way of alerting a team member of any impending danger.
Pile Driving Applications
Do you want to install a structure in an area where the subsurface conditions would otherwise not support a structure? That’s the kind of environment where you can use piles with the help of a pile driver. The most notable application of pile driving is in the construction industry. Contractors use the mechanical device to build piers, buildings, and bridges.
The good thing is that there is a pile driver for every application capacity. For instance, the modestly-sized pile drivers by Everstar are perfect for solar projects, highway guardrail projects, and vineyard guardrail projects. They are highly versatile, serving functions such as piling, rotary drilling, impact drilling, screwing, pile pulling, and so on. The availability of different accessories adds to this versatility.
- Other types of pile-driving applications are:
- Oil and gas industry
- Marine projects
- Sizeable infrastructural projects
In Conclusion
This article has covered the definition of pile driving, the different types of pile hammers and their components, and the several challenges and solutions of pile driving.
By understanding these aspects of pile drivers, contractors can build small and large structures with the same confidence. They can identify project issues and implement optimum solutions for construction activities.
Everstar is a dependable provider of reliable and efficient pile driver machines built for precision, durability, and efficiency. Contact us today to learn more about our technologies and get an instant quote.