The major part of understanding how a Rotary Drilling Rig works is getting familiar with the complex tools and accessories that make the operation possible. Knowing intricate details about what goes behind the rig will help businesses make better-project-related decisions.
So, here we break down the list of the most critical Rotary drilling rig accessories and their functions. Let’s get started.
What is a Rotary Drilling Rig?
Rotary Drilling rigs are the machine of choice in modern-day drilling applications. They are used everywhere, from mineral exploration, construction foundations, geotechnical sample extraction, and well drilling.
It penetrates the earth’s surface by applying downward pressure (mostly the weight of the components) with a rotating drill bit that shears through the rock formation.
Unlike traditional percussion drilling (hammering) or manual excavation, the rotary systems are in a league of their own with superb efficiency, speed, and drilling capacity. Generally, you’ll see Mud rotary, Air rotary, Dual Rotary, and Reversible rotary drilling rigs available in the market.
Why Is It Important To Understand Rotary Drilling Rig Parts?
Drilling projects are long-term excavation tasks with ever-changing project needs and requirements. Such project needs are handled using various rotary drilling equipment, rotary tools, and spare parts.
Each Rotary drilling accessory plays a critical part in the rig’s functionality, and building a familiarity with them will ensure safety, better efficiency, and overall enhanced performance.
The rig components are mostly selected on the basis of performance, with some exceptions, of course, while the selection of drilling bits and tools depends highly on location, rock formation, and ground base.
We also recommend thorough inspection and testing of Rotary drill accessories prior to the final billing stage, as this will help you get the best tools and equipment for your project.
Must Know Rotary Drilling Rig Accessories
With how complex and big Rotary drilling rigs can get, it’s only natural that the machine would have hundreds of intricate accessories.
To simplify things, we have categorized the most important components into groups of systems that make up a typical rig.
I. Rotary Drilling System
Featuring all major components that are responsible for the rotational force and linear motion of the rig.
(Courtesy of Gregory King, Professor of Practice, Petroleum and Natural Gas Engineering, The Pennsylvania State University.)
1. Swivel
The swivel is a major linking component connecting the hoisting, rotary table, and mud circulation systems.
Its design allows it to hold the weight of the hoisting system while freely rotating the drill string and, consequently, drilling a bit at the bottom. It also provides drilling fluid sealing for the circulation system.
2. Kelly
Kelly is a square (or hexagonal) pipe just below the swivel that transmits the rotational torque through bushings to the Rotary table. The Kelly threads are designed to give normal right-hand rotation to the drill string.
However, in the latest Rotary rigs, especially in Dual Rotary drilling, the Kelly, its bushings, and rotary table are replaced by the top drive.
3. Drillstring
Drillstring simply connects the equipment above the earth’s surface to the drill bit down below. It isn’t a component itself. Rather, it’s a combination of interconnected drill pipes and bottom hole assembly (BHA).
4. Rotary Table
The classic Rotary drills all had a Rotary Table, which is the main driver consisting of swivel, Kelly, and drill string.
Primarily, this platform facilitated the rotation of the drill string and evenly distributed mechanical force. In the latest machines, top drives have taken the role of rotary tables and are driven either by hydraulics or electric motors.
5. Drill Bit
The main tool that shears and breaks through the tough rock formation during drilling is much like the one we see in hand-held drills but on a bigger scale.
These cutting tools are attached at the bottom of the drill string and come in various shapes and sizes. Common examples include the Tri-cone bit and Fixed cutter bit.
II. Circulation System
Components responsible for efficient drilling fluid circulation.
6. Rotary Hose
Rotary hoses are special-grade pipes that maintain the leak-free circulation of mud or any type of drilling fluid.
7. Mud Pits
Mud pits are the storage tanks where the drilling fluid mixing takes place.
Usually, an operator observes the ratio of the mix. The rotary hoses help transfer the fluid from mud pits through the swivel and down the drill string all the way to the drill bit, where it exits via tiny holes and aids the cutting process.
The fluid moves back up the hole due to intense pressure, carrying the cutting with it, and passes through a Shale shaker, Desander, and Desilter, where solids are removed and filtered drilling fluid is poured back into the mud pit.
8. Mud Pumps
Mud pumps are the main driving force between drilling fluids. Typically, they are single-action or double-action reciprocating dual-cylinder pumps. In Air Rotary drill it’s replaced by air compressors.
III. Hoisting Accessories
High-performing hoisting accessories keep all components moving smoothly.
9. Derrick
A derrick or mast is a support framework of bars and poles that help carry the oil rig equipment. All the components we discussed above, from the crown block to the drill bit and drill pipe, are supported within the derrick structure.
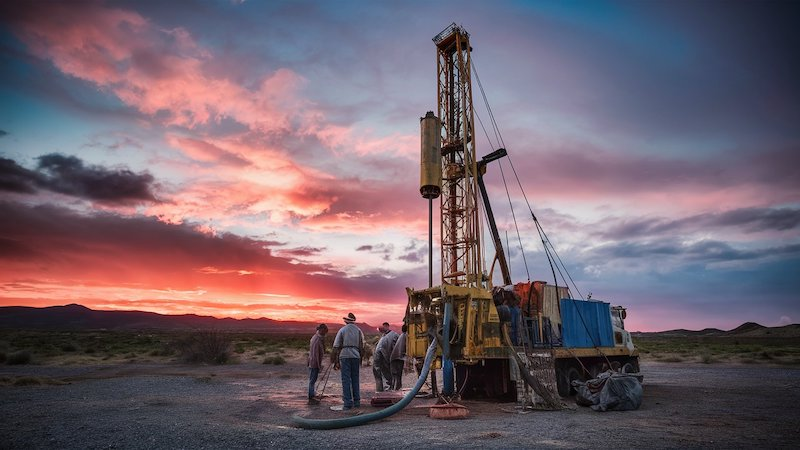
10. Drawworks
Drawworks is simply a winch that reels the hoisting cable in and out, carrying the traveling block and swivels or, in the case of contemporary Rotary rigs, the entire Top-drive mechanism. Modern-day draw works include cutting-edge electromagnetic brakes as well.
11. Crown and Traveling Block
Crown and Traveling blocks are composed of cables strung around a pulley system that help all the Rotary rig accessories move up and down the derrick. They drive power from the draw works.
IV. Well Control System
The complex rotary rig machinery requires a robust control system to prevent the uncontrolled release of high-pressure fluids (oil or gas) from the subsurface.
This is particularly catastrophic in oil and gas wells, where any spark can ignite the fuel and cause an explosion. The tragic disaster on the Deepwater Horizon was due to a failure in the control system.

12. Blowout Preventer (BOP)
The Blowout Preventer mechanism is a system of valves powered by hydraulics that separates the subsurface from the rig and acts as a safety net in case of any mishap. The BOP may trigger due to various reasons, such as insufficient mud weight density, improper mud replacement, lost circulation, etc.
13. Accumulator
The accumulators store pressurized hydraulic fluid and gasses that provide backup power to the Blowout preventer in the event of Power system failure.
V. Power System Accessories
The main driving force behind the rotary rig.
14. Engines and Generators
Rotary drill drives power from internal combustion engines or, more specifically, diesel engines, which then run DC electric generators and provide power to the rig.
15. Fuel Storage
Historically, coal was used to power the Rotary rigs, but in modern technology, diesel and other petroleum-based fluids are used and stored in the fuel storage tank.
How do you Choose Rotary Drilling Rig Parts?
Every project has specific drilling tool requirements based on factors such as rock formation, drilling depth, drilling process, and budget. Selecting the appropriate rotary drill parts will ensure the long-term success of your drilling operations.
Here’s how you can do it.
A. Conduct Research
Conducting proper research is critical to set the base right for the project.
a. Geological Survey
Start with a comprehensive geological survey of the drilling site. This includes studying surface composition, maps, and reports. Also, identify any potential geological anomalies like extreme hard rock formation, loose soil, or unstable ground.
b. Formation Analysis
Analyze the surface formation by carefully looking into rock hardness, abrasiveness, porosity, and permeability. Knowing the type of formation will help you select the right drilling tools for the job.
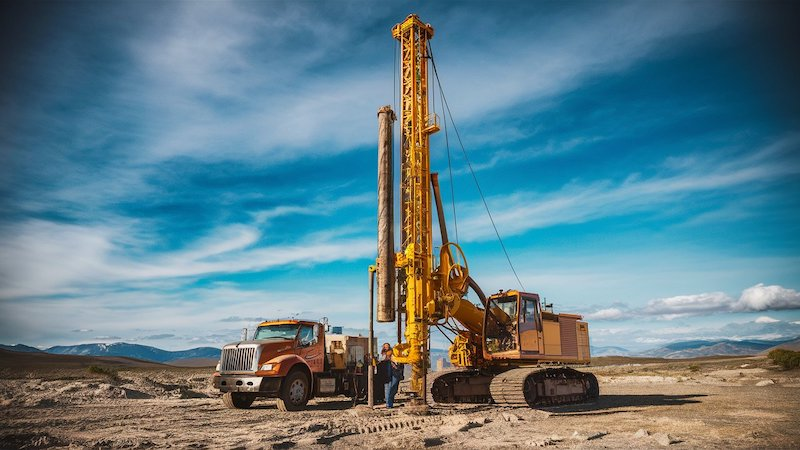
c. Risk Mitigation Strategies
Develop a risk mitigation strategy to address potential drilling challenges and operational disruptions. Make a contingency plan for drilling equipment failure, stuck pipe incidents, or the occurrence of unexpected geological conditions during operation.
B. Consult the Expert
Consulting expert geologists, drilling engineers, and industry surveyors will help refine the drilling plans and optimize operational parameters.
C. Ensure Compatibility
By ensuring compatibility between Rotary drilling accessories, tools, equipment, and spare parts, you can optimize the project’s performance and reduce potential downtime.
Routine Maintenance of Rotary Drilling Rig Accessories
Regular maintenance is absolutely critical for prolonging the life of rotary drilling accessories and preventing costly breakdowns. Here are the key aspects of routine maintenance.
- Inspect accessories regularly for signs of wear, corrosion, or damage.
- Clean and lubricate moving parts to reduce friction and prolong service life.
- Replace worn-out parts promptly to avoid equipment failure and ensure safe operation.
- Schedule routine servicing and follow the manufacturer’s guidelines for maintenance intervals.
Conclusion
By knowing the details of entire rig accessories, you’ll be better equipped to manage and purchase spare parts and schedule their routine maintenance and servicing.
We also talked briefly about the selection of such accessories and how businesses can come up with the right strategies for optimal performance. With this knowledge, you’ll also be better prepared to negotiate with manufacturers of drilling rig tools.
Achieve Brilliance with Everstar: Your Partner for Cutting-Edge Drilling Solutions
For over a decade, Everstar has been a trusted partner in the construction and drilling of industrial projects worldwide. Our advanced machines, such as the Exploration Rig Drilling Machine and Hydraulic Water Well Drilling Rig, set the standard for exceptional performance.
And with top-notch accessories, competitive spare parts pricing, and unparalleled after-sales service, our cutting-edge technology offers unmatched value. Ready to elevate your business? Reach out for our Free project consultation today.