Rotary drilling rigs are among the most sought-after drilling tools in the modern-day industry, thanks to their extreme efficiency and versatility, ranging from mineral exploration to digging oil wells.
In this detailed guide, we explore the working principle, types, and factors that any business should consider when acquiring a rotary drilling rig to maximize its success.
Let’s dive in.
What is a Rotary Drilling Rig?
A rotary drilling rig is a machine that conducts drilling operations to excavate the earth’s surface. It is commonly found in open pits, mining, quarry settings, construction, mineral exploration, and oil and water well applications.
It utilizes both downward pressure and rotary motion of a drill bit to cut through the soil formation, making it a much more efficient and cost-effective drilling process compared to traditional percussion drilling, which only uses impact force.
However, rotary drilling isn’t a new concept, and some evidence shows it dating back to the Egyptian civilization in 3000 BC, but we only harnessed its true potential after the age of engines and hydraulic and pneumatic systems.
In Texas in 1901, Captain Anthony F. Lucas drilled the Spindletop oil well using a rotary drilling method, allowing for deeper and more efficient drilling compared to older methods. It is considered one of the most significant events in history, kickstarting the American oil age.
Since the early 1990s, we have seen more advancements in rotary drilling technology, allowing for deeper excavation while reducing costs and environmental hazards.
A rotary drilling rig can cut vertically straight through both soft and hard rock formations and achieve depths of up to 3000 meters while maintaining a bore diameter ranging from 203 mm to 445 mm.
Working Principle Of Rotary Drilling Rigs
Many types of rotary drilling rigs are used in the industry, which we will discuss later, but the main working principle is the same across all the varieties.
The rotary drilling involves downward thrust coupled with a rotating motion of the drill rod. The rod encompasses powerful torque and rotates at a speed between 50 to 120 rpm.
The weight of the drill rig itself is sufficient enough to provide the downward pressure, while the rotary motion is achieved by a diesel or gasoline engine.
Different types of drill bits are used depending on the soil formation, but the two most common are three roller-cone bits and fixed cutter bits, also known as polycrystalline diamond compact bits (PDC).
They are covered with teeth and buttons that crush and shear through the earth’s surface. The three cones move freely and work as a planetary gear system, drastically increasing the drill rod’s performance.
As the drill rod moves forward, a casing is added and inserted using either a hammer or a separate motor drive, as seen in “Dual rotary” machines.
Another important feature of rotary drills is the use of drilling fluids or compressed air. Drilling fluid, also known as “Mud,” is pumped through the drilling rod, which then escapes through the bottom of the drill bit and moves upward, carrying the cuttings with it.
It also serves as a lubricant, preventing excessive wear and coolant for the drill rod, and provides stability to the borehole.
Types of Rotary Drilling Rigs
Rotary drilling rigs come in different shapes and sizes tailored to specific applications.
Here are the four most prominent rotary drilling types used in the industry.
Based on Drilling Fluid
Rotary drills can be classified on the basis of drilling fluid used as follows.
1. Air Rotary Drill
Air rotary drill utilizes compressed air or gas to remove the cuttings from the borehole. However, the rest of the rotary rig works the same as any other machine. It’s suitable for softer formations.
2. Mud Rotary Drill
The mud rotary drill utilizes drilling fluid, commonly known as mud, to facilitate the drilling process. It is much more efficient in removing cuttings, cooling the drill bit, and stabilizing the borehole.
Drilling fluids are called “mud” due to their similar appearance to earth mud, but in reality, they are composed of natural and synthetic materials such as baryte powder, calcium carbonate (chalk), etc.
Mud rotary drills are primarily used when borehole integrity is critical because the mud applies a thin layer of cake on the surface, sealing any pores and other openings.
Reversible Rotary Drill
The reversible rotary drill features an excellent design that can reverse the flow direction of drilling fluid.
Typically, in a conventional mud or air rotary drill, the fluid flows through the center of the drill bit, emerges from the bottom, and moves upward through the side opening, carrying the cuttings with it. However, the reversible rotary drill reverses the flow from the bottom back into the column within the drill string and is pumped to a separate container or desired location.
Reversing the direction of drilling fluid offers several advantages, such as disposing of the drilling fluid in a controlled manner.
In conventional direct rotary systems, the fluid simply expels through the borehole from the top, causing a mess for workers and the environment. However, with the reversible rotary drill, this is not an issue.
Reversible rotary drills are mostly used to drill shallow but large diameter boreholes, which can get more than 3 meters wide. Although Reverse circulation is a good alternative to direct circulation rotary drill, the equipment is pricier.
Dual Rotary (DR) Drill
Dual rotary drills are powerful tools used in the toughest formations around the globe. Unlike regular rotary drills, the dual rotary features two rotational drives.
The first drive powers the drill bit conventionally, while the second one provides rotational torque to the casing, simultaneously drilling the hole and advancing the casing. In traditional rotary drills, the casing is moved through impact force provided by constant hammering action, which is inefficient and noisy.
A carbide-studded shoe is attached to the casing, making the movement smoother and allowing for quicker penetration of the rock formation. Typically, drill bits and casing rotate in opposite directions for maximum efficiency.
The two drives, upper and lower, operate separately, meaning the casing and drill bit positions may not be synchronized. Once the casing reaches a certain height, the drill continues to move and work as a regular air or mud rotary drill.
The main advantage of a dual rotary drill rig is the elimination of the need for a casing hammer, which causes serious noise pollution—a considerable issue in residential neighborhoods.
Additionally, casing hammers are inefficient in larger depths, as the constant stress from hammering can accumulate fatigue in the material, resulting in damage.
Additionally, when the casing encounters rock boulders buried deep in the earth, its motion halts. Continued hammering can either break the casing or cause borehole deviation, resulting in wasted time, effort, and resources invested in the operation. In contrast, the rotating carbide shoe-fitted casing can easily cut through tough rock formations.
Dual rotary drills are designed to drill extremely straight and vertical holes, making them very useful in construction applications.
Pros and Cons of Rotary Drilling Rigs
There isn’t one size fits all for rotary drilling rigs, as each type comes with its unique application.
Here, we briefly discuss the major pros and cons of each.
Rotary Drilling Rig guide.csv
Rotary Drill Type | Pros | Cons |
---|---|---|
Mud Rotary | Suitable for unconsolidated formations like sand and gravel. | It is not as efficient in hard rock formations. |
Effective in less stable geological conditions. | Requires frequent replacement of drill bits. | |
Provides good core recovery for analysis. | Slower drilling rate compared to other methods. | |
Air Rotary | Ideal for drilling in hard rock formations. Provides fast drilling rates. | Limited effectiveness in soft and unconsolidated formations. Requires significant air supply and management. |
Less prone to bit wear and damage in hard formations. | Creates large amounts of dust and debris. | |
Dual Rotary | Suitable for challenging formations, including hard rock and unconsolidated materials. | More complex machinery and setup compared to other methods. |
Provides efficient casing advancement simultaneously with drilling. | Higher initial investment cost. Requires skilled operators for optimal performance. | |
Offers versatility for various geological conditions. | ||
Reversible Rotary | Reverses the flow direction of drilling fluid, allowing controlled disposal. Minimizes mess for workers and the environment during drilling. | Equipment cost is higher compared to conventional direct rotary systems. |
Suitable for drilling shallow but large-diameter boreholes. | It may require additional training for operators. | |
Potential for increased maintenance needs due to complexity. |
7 Major Components Of A Rotary Drilling Rig System
Rotary drilling machines are state-of-the-art drilling tools with complex machinery and design.
For the sake of ease, we are going to briefly discuss the seven major components of conventional rotary drilling rigs.
1. Drill String
Drill string refers to the combination of multiple drill pipe columns that transmit drilling fluid to the bottom and provide rotational torque to the drill bit from the earth’s surface powered by the engine.
2. Drill Bit
It’s the cutting tool at the end of the drill string that does all the drilling. Different types of drill bits are used depending on the rock formation and geological conditions.
3. Rotary Table
A series of mechanical components that provides stable rotation to the drill string and transmits the necessary force onto the drill bit.
4. Mud Pump
The Mud rotary drill has a combination of mud pump and rotary hose that circulates drilling fluid down the drill string and back up through the borehole, carrying rock cuttings with it.
In air rotary drills, this circulation system is replaced by an air compressor.
5. Hoisting System
Another multi-component system is used for pulling back drill strings and casings. It consists of a derrick, crown block, drill collars, and traveling block with several pulleys and chains. In advanced rotary drilling rigs, such systems operate using hydraulic systems.
6. Control System
Control systems are like the brain of the drilling rig, monitoring all the operations and related drilling parameters, mud flow rate, and hoisting operations.
7. Power System
Diesel engines or electric motors are typically used to power the drilling rig, including lights, pump, hoisting system, and rotary table.
Applications Of Rotary Drilling Rigs
Rotary drilling has numerous applications across different industries. Here are some examples.
Mineral Exploration
Rotary drilling helps extract core samples from the earth’s subsurface, which is otherwise impossible with traditional drilling systems as they can only go to certain depths.
The samples are then studied by geologists and mining companies to identify the presence of valuable minerals and stones.
Oil and Gas Exploration
Rotary drilling is a suitable method to drill oil and gas wells on either offshore or onshore surfaces.
Water Well Drilling
Whether it’s domestic, agriculture, or industrial, the rotary drill is a go-to option for creating water wells. The high depth capacity and rotary drill help access groundwater in deep aquifers.
Geotechnical Investigation
Geotechnical engineering refers to analyzing subsurface conditions of construction sites, including soil composition, rock formation, groundwater levels, etc.
Rotary drills are an excellent option for this work, as the information gathered helps in designing footings, foundations, and other infrastructure bases.
Environmental Site Assessment
Rotary drilling helps collect soil and groundwater samples for contamination assessment.
Construction and Foundation
Rotary drilling can provide robust, stable, and vertical boreholes that are perfect for installing piles and retaining walls that ensure structural stability.
Blast Hole Drilling
In mining and quarrying operations, rotary drilling helps create blast holes for explosives.
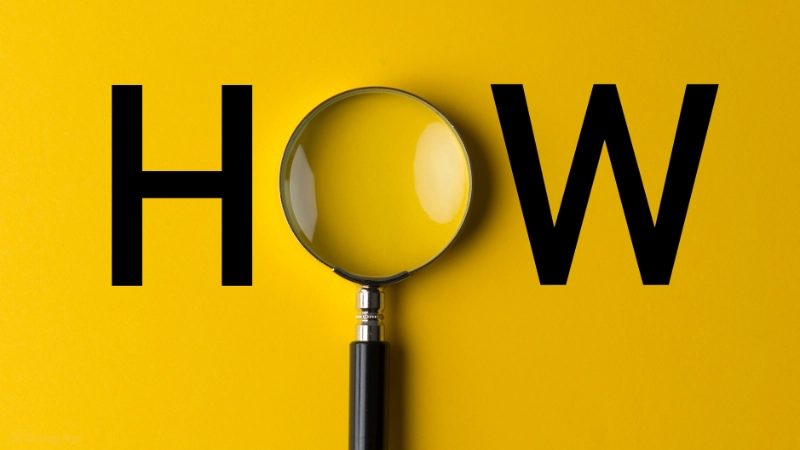
How To Choose A Rotary Drilling Rig?— 7 Critical Factors
If your business has decided to purchase or hire higher rotary drilling services, then considering these factors will help you streamline the process.
1. Geological Conditions
First, the geological conditions and rock formation where the operation needs to take place should be evaluated. Though rotary drills are versatile, some types excel in certain applications.
2. Drilling Depth
Determine the expected depth of the drill, as some drills (like Dual Rotary) are more capable of reaching greater depths, while others, like Reversible Rotary, are better suited for shallow drilling but wider boreholes.
3. Drilling Rate
Drilling rate and speed are other important factors to consider. What you need is a complete feasibility report about the nature of your project, which will help you find the machine that matches your requirements.
4. Environment Regulation
Be mindful of the environmental rules and regulations of the area you are working in. Common restrictions include managing noise pollution, emissions, and drilling fluid discharge.
5. Equipment Size and Mobility
You must consider the available space for operation in your designated area. Confined spaces or remote locations require special care regarding the transportation and setup of drilling rigs.
6. Budget and Cost Consideration
The company must consider all the costs of purchasing or renting a drilling rig as well as the operational costs. Choose the machine that offers the best value for money while meeting your project requirements.
7. Manufacturer Reputation and Support
Lastly, the reputation of the rig manufacturer and its previous track record must be properly checked. Look for a company that is known for high-quality, reliable rigs and excellent customer service. Additionally, warranty coverage, spare parts availability, and after-sale technical services should be considered.
Conclusion
We’ve covered the working principles, applications, and selection criteria for rotary drilling rigs comprehensively, focusing on their industrial applications and targeting businesses.
Whether you intend to purchase a rotary rig or plan to hire services, having a basic understanding will enable you to communicate effectively with the manufacturer and choose the right product for your project.
Unlock Innovation with Everstar: World Leading Manufacturer of Pile Drivers and Drilling Machines
Everstar is a leading high-tech enterprise with expertise in manufacturing cutting-edge solutions for highway construction and well drilling. We have assisted our clients in their businesses for more than a decade, establishing ourselves as a trusted name in the field.
Our top-of-the-line rotary drills include the Exploration Rig Drilling Machine for Geological Prospecting and the Hydraulic Water Well Drilling Rig for Well Construction. Our technology epitomizes excellence, and it is available at competitive prices with great value-added services. So, are you ready to take your business to new heights? Contact us today for a free consultation on your project.