So, we’ve compiled a list of commonly used water well drill bits and the factors that must be considered to choose the right tool. Let’s dive in.
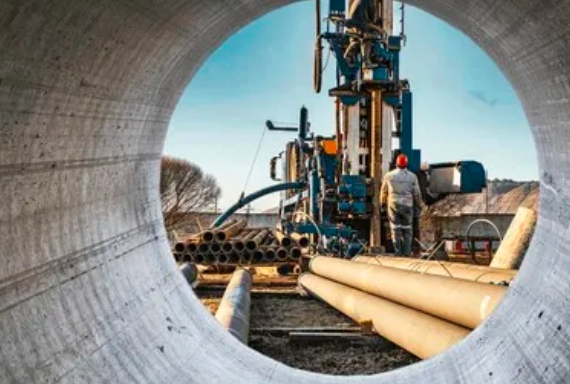
Why are Drill Bits Important for Water Well Drilling?
The selection of the right drill bit is pivotal in the success of any water well drilling expedition. Sometimes, multiple types of drilling bits are used to dig a single borewell because each type has unique capabilities.
Some major factors that are directly affected by drill bit actions and its type are:
- Drilling speed and Rate of penetrations (ROP) of borewell.
- Wear and tear of a drill bit.
- Overall drilling cost of the project.
- The success of the drilling project.
- Maintaining borehole stability.
- Drilling accident probability and borehole stability.
Hence, choosing the optimal drilling location and considering the geology and logistics of the place are critical for a successful well-water drilling project.
How to Choose the Right Water Well Drill Bit?
Many factors contribute to selecting the right water well drill bit, including the experience gained from working in the field for years.
Here are the critical factors that any drilling service company must account for before purchasing the drill bits.
1. Geological Condition
It’s a no-brainer that the geological condition is a major determining factor for the selection of drill bits. Surveyors estimate rock formation in a particular area and conduct drill bit research.
The upper earth’s surface usually has overburden, a combination of clay, sand, silt, and shell. As the hole digs deeper closer to the aquifer, hard rocks may block the way. Drill bits are designed to cater to different earth formations.
2. Well Diameter and Depth
Water wells have different diameters as the initially bigger holes are dug, and then eventually, the drill bits become leaner. Similarly, as the hole gets deeper, the rock formations become tough and abrasive, which can accelerate the wear and tear of the tool.
There is a “Cost per Foot” equation that helps estimate the price of a drill bit depending on the rotation per minute (RPM) it can achieve and the distance it can penetrate before tool failure.
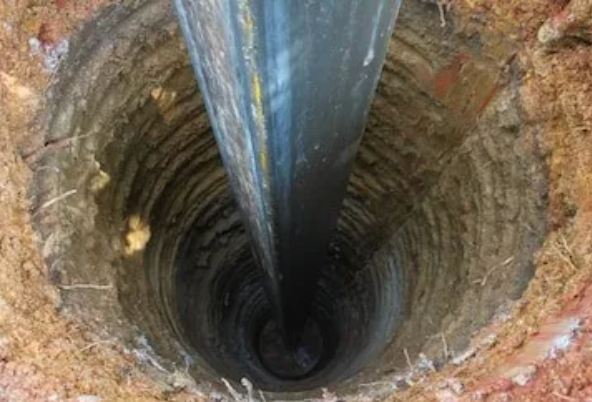
3. Budget Consideration
Drill bits come at varying prices, which, of course, plays a role in deciding the type of drill bit required.
Apart from the upfront price, the total cost spent during downtime for replacing the worn tool is also considered. Some heavy-duty PDC drill bits last longer but have a much higher upfront cost.
The cost also depends on the type of material used to build the tool. Some water well drilling rig companies get expensive drill bits on rent instead of buying a new one, which is more economical for the business.
4. Drill Bit Testing
If the drilling bit supplier or manufacturer allows it, you can test the drill bit for water well drilling before buying to ensure you have the best product.
The bit’s functionality depends on the drill equipment weight and the RPM it can achieve, considering the friction it faces in any rock formation.
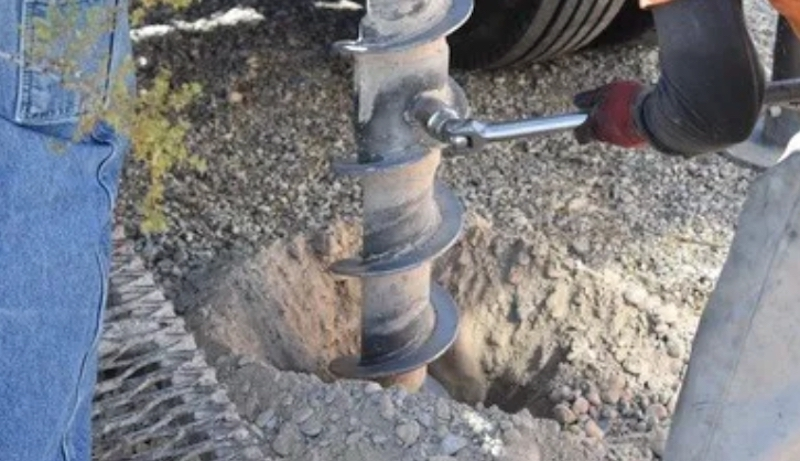
5. Consult with Experienced Professionals
The on-field experience matters, and hiring experienced surveyors or investing in a consulting firm can save you a lot on the drilling water well costs in the long run. As drill bit directly affects the success of your project.
6 Types of Water Well Drill Bits Mostly Used in Industry
Now that we know the basic factors that help in choosing the right water well drill bit, let’s explore some of the options available on the market and their unique characteristics. We’ll discuss the most commonly used tool bits in the water well drilling industry.
1. Milled Tooth Tricone Roller Bits
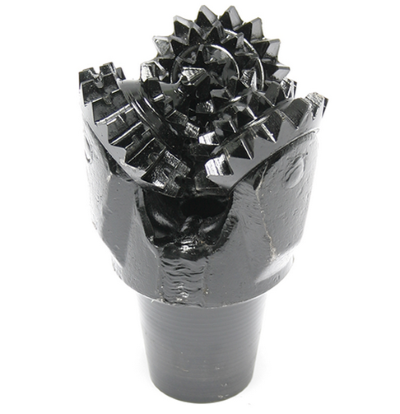
These bits have rotating cones with hardened teeth, usually made with steel, that crush and grind the rock formations as they rotate. They are primarily used in softer rock formation and are economical to use in most cases. The rolling action of teeth gouges the rock formation into fine cuttings.
Pros:
- Suitable for softer rock formations
- Good Rate of penetration
- Economical
Cons:
- Roller bearing susceptible to wear
Insert Tricone Bits
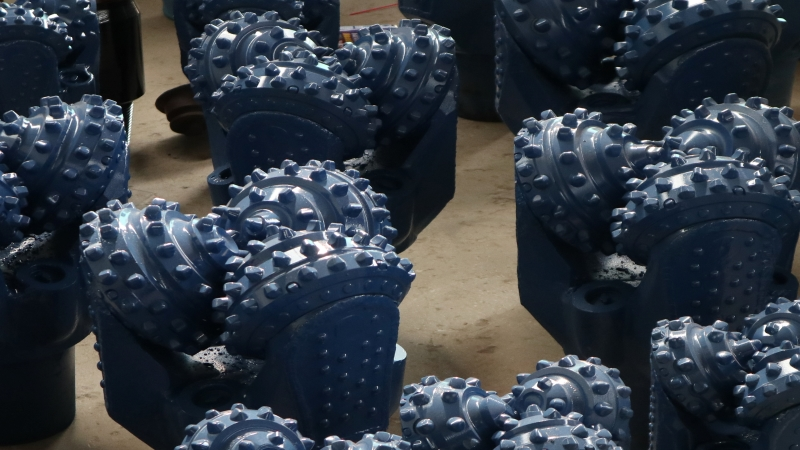
Similar to roller cone bits, tricone bits have three rotating cones but with inserts made with tungsten-carbide steel, which is more durable than steel.
The tungsten carbide inserts (TCI) bit crushes and gouges the rock underneath the surface. It offers versatility for drilling through various formations. TCI bits come in a variety of shapes and sizes and, due to their appearance, are also called button bits.
Pros:
- Suitable for medium to hard and abrasive rock formations
- Good Rate of penetration
- Economical
Cons:
- Roller bearings are susceptible to wear
2. PDC (Polycrystalline Diamond Compact) Bits

PDC bits are fixed cutter bits featuring diamond-enhanced cutting tips that provide excellent durability and efficiency in drilling through hard formations.
This drill type has no moving parts, and it works by shearing the tough rock formations. Some common examples are PDC, Natural Diamond, and Impregnated bits.
Pros:
- Shear through extremely hard rock formations
- Higher drilling speed.
- Longer life span
Cons:
- Higher upfront cost.
3. Drag Bits
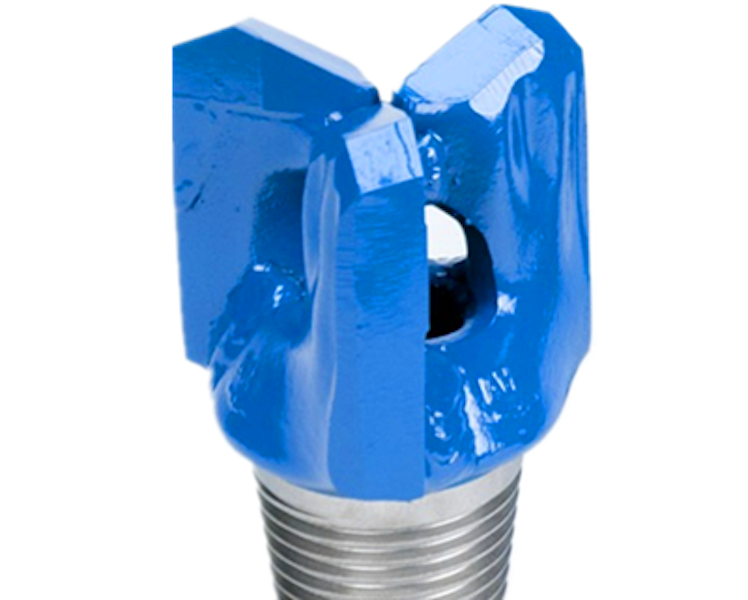
Step drag bits contain multiple fixed blades featuring various cutting angles. These bits are best suited for digging the hole initially, and depending on the drag bit type, they can cut through soft to hard rock formations.
Pros:
- Suitable for a wide range of hard rock formations
- Higher drilling speed
Cons:
- Not suitable for very hard rock formations
4. Auger Bits
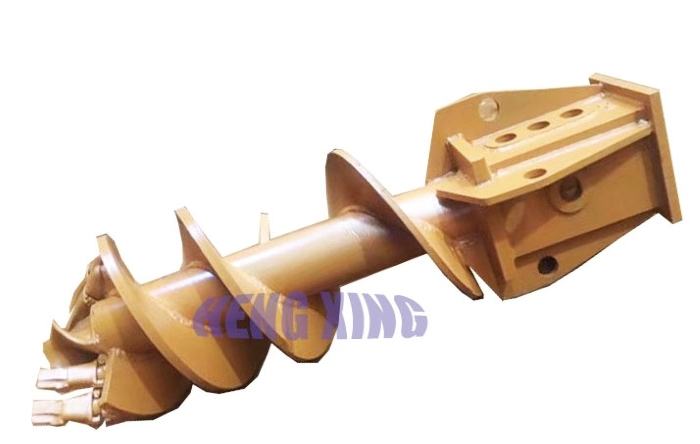
Auger bits have helical blades or screw-like threads that excavate loose materials and soil, making them suitable for shallow water well drilling in softer formations. Some of its types include single/double cut flat and rock augers.
Pros:
- Good for soft to medium rock formations
- Higher drilling speed
Cons:
- Not suitable for very hard rock formations
5. Claw Bits
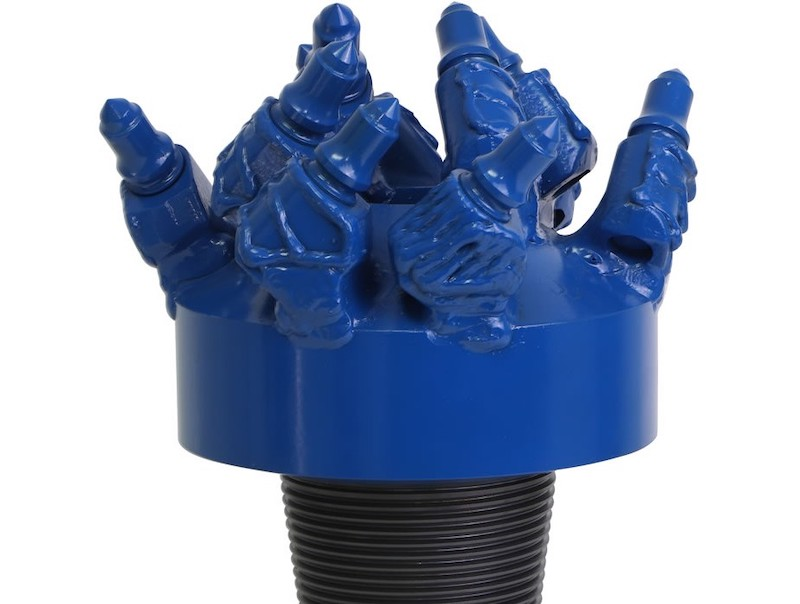
Claw bits feature unique finger-shaped cutters that rip through the rock formations. These finger blades are replaceable and prevent over-torquing, leading to a longer life span. These bits work effectively in dense clay formations.
Pros:
- Best suited for dense clay formations
- Higher Rate of penetration.
Cons:
- Limited area of applications
6. Reamer Bits
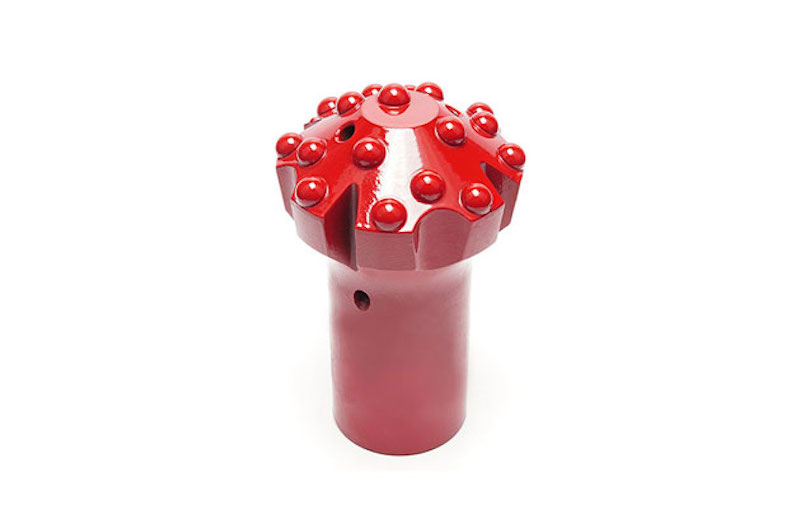
The reamer bits are usually required to broaden the existing borehole and bring stability to it. Mostly used on softer rock formations like clay.
Pros:
- Good for the clay rock formation
- Higher drilling speed
- Inexpensive
Cons:
- Limited usage
Maintenance and Care for Drill Bits
Drilling operators should follow these maintenance practices for optimum performance, longevity, and reliability of their drill bits.
1. Regular Inspection
Always conduct thorough visual inspections of drill bits before and after each use to check for signs of wear, damage, or deformation. It also prevents unnecessary downtime and greatly reduces drilling costs.
2. Sharpening
Poor Rate of penetration (ROP) and drilling performance are clear indicators of blunt tools. Sharpen or recondition drill bits as needed to maintain cutting efficiency.
3. Replacement
Sharpening the tool helps to some extent, so when the time comes, replace worn or damaged drill bits promptly to prevent poor drilling performance, potential equipment damage, and downtime losses.
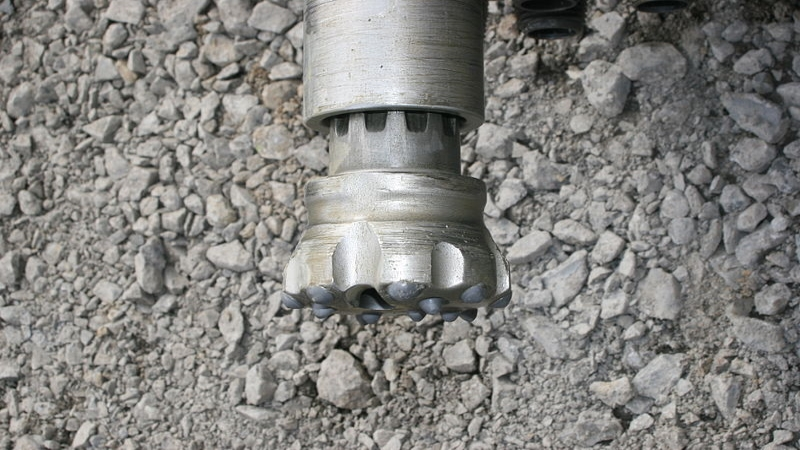
4. Storage
Make sure to store drill bits in a clean, dry environment, away from moisture, extreme temperatures, and corrosive substances.
5. Training and Education
Make sure the drilling operators are properly trained in drill bit maintenance and care procedures to maximize the lifespan and performance of the equipment.
Methods and Steps for Water Well Drilling
Let’s explore the process of water well drilling briefly.
1. Site Assessment
First, the drilling company identifies suitable drilling locations based on geological data. They consider groundwater depth, quality, and accessibility, as well as regulatory requirements.
2. Equipment Setup
Next, the company sets up the drilling rig according to manufacturer guidelines. The operators ensure proper installation and setup of water well-drilling rigs, pipes, and accessories.
3. Drilling
Once the equipment is ready, the drilling service provider initiates drilling using selected methods (rotary, percussion, etc.). Expert operators monitor progress, adjust parameters, and drill to the desired depth.
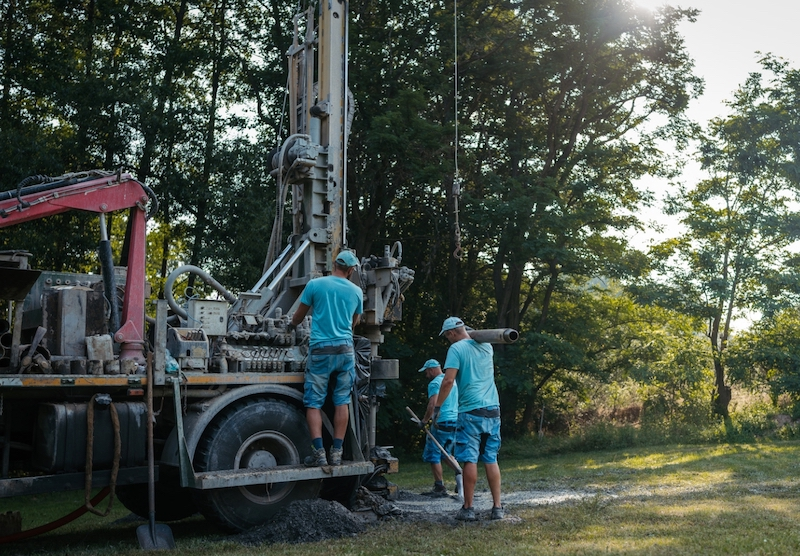
4. Casing Installation
Once the drilling tool hits the groundwater pore space, the mechanics install casing to prevent borehole collapse and eliminate groundwater seepage. In deeper wells, this process is done simultaneously with drilling.
5. Pump Installation
Finally, the water pump and associated equipment for groundwater extraction are installed.
6. Testing and Maintenance
The drilling company conducts the pump tests to assess well performance. They also monitor groundwater levels and quality for any changes over time.
FAQs
1. How Do Drillers Know Where To Drill For Water?
Drillers use geological surveys and groundwater mapping to estimate the right location to drill well water. These are called estimates because there is no way to be 100% sure about the presence of groundwater.
2. What’s Better: Black Oxide Or Titanium Drill Bits?
Black oxide coating helps with the corrosion resistance of drill bits, but when it comes to durability and heat resistance, the titanium drill bits are better. However, titanium drill bits are pricier.
Conclusion
By going through this guide, you’ll be well-versed in the basics of water well drill bits and the factors your business needs to consider before investing in high-performing drill bits.
Apart from drilling tools, ensure the drilling machine manufacturer offers value-added services like maintenance and warranties for tools.
Take Your Drilling to the NEXT Level With Everstar Drill Bit!
For more than ten years, Everstar has been a reliable ally in global industrial construction and drilling projects. Our state-of-the-art drilling machines and equipment guarantee exceptional performance. Coupled with competitive pricing of spare parts and exceptional after-sales service, our technology provides unparalleled value.
Ready to take your well-drilling project to the next level? Contact us today for a Free project evaluation.